|
Losses?
Why there is almost no connection
between off-gas losses and annual energy consumption
The end of the year is always the time to read off and add up the numbers on the meters to know how you have managed. In heating, this is called annual energy consumption. Customers of gas provider can simply read off this consumption (in kWh) from their bills, whereas owners of oil heating systems have to calculate the quantity they have used from difference beetween tank levels or simply regularly reading off their oil meter.
This picture shows in an overview what happens when the energies have been combusted and have passed through the piping into your radiators. Seen over the course of a year, only 60...70% of the energy you had in front of the burner arrive at the radiator; this is the annual utilisation ratio of your system:
Over the year, about 40% of the energy you have paid for are lost in the boiler and the piping system.
[Source: IWO, Oil heating systems]
It is easy to calculate: annual utilisation ratio.
Qzu is the quantity of oil or gas in kWh,
Qn is the useful work in kWh read off from your heat input meter.
|
We try to give you an overview of when losses occur and how to cut them. With the right improvements this will get your heating system running more efficiently and will cut the amount of energy you are using.
Our main focus is to find out the significance of those suspicious off-gas losses, which are so important that they are regulated by the government here in Germany. The off-gas is annually measured by government officials, even though this contravenes §13 of our German Basic Law (domestic inviolability). The measurement can only show the burning efficiency when the burner is on - which is always more or less what the manufacturer specifies.
Don't confuse different kinds of data!
Burning efficiency is a momentary value which only applies when the burner is on, ie only during part of your annual consumption time. On the other hand, your annual consumption is a statistically summed value, resulting from a large number of small daily consumptions over the year.
We wish to highlight the frequently made error that you cannot put these differently measured values into the same equation. Multiply or add them and you will only get nonsense. The following "calculation" is put out by the boiler manufacturer Buderus to get people to buy new boilers:
Off-gas losses[%] * annual consumption = unused and lost fuel energy
This is incorrect: statistical experts will tell you that equations containing measurement values which fluctuate are only valid if those measurement values are captured during the shortest measurement periods or those of identical duration.
[Database: Year 1999: Daily values for gas consumption displayed versus daily average outside temperature.
Source: DTS - Datentechnik Stöckl, 94227 Zwiesel]
|
The diagram on the left will perhaps make clear that there are 'slight' differences between the momentary values for off-gas loss and the daily mean values which form annual consumption from the sum of the cluster of single values :-)
The off-gas loss is mainly calculated via the off-gas temperature. The Buderus equation would be valid if the annual off-gas temperature mean were inserted. Because these off-gas temperatures are only transient peak values, these peaks will be evened out by the idling temperature which applies 83% of the time. Correct application of the mean would result in a off-gas temperature of about 45...50ºC.
|
Annual energy consumption results from three recurrent heating cycles:
burner operation, idle and cooling down and burner ignition (phase of particularly high loss).
- Minimal off-gas loss would be extremely important for permanently running burners which have to generate heat or steam for 80...100% of the year (not applicable for the low 17% running time in residential buildings).
- Insulation is important for both boiler operating modes, permanently running burners and heating systems of residential buildings: in absolute numbers its importance in the case of a permanently running burner pales in comparison to off-gas loss. For appartment heating, insulation is about six times more significant than off-gas loss.
- Usually the house is the heating recovery system built around the chimney: those able to read German might like to read about this 'forgotten' heat recovery at
Dr. Luther's Website.
More details below:
[ Contents ]
2. Boiler losses
...when the burner is running
When a burner generates heat, the boiler acts as a heat-exchanger, splitting the heat flows into
- the part known as boiler losses and
- the part which is meant to be distributed as useful heat.
In this phase, the annual energy consumption comprises losses or useful heat of the individual components while running:
Q year = Q boiler + Q distribution + Q N(useful)
or in more detail
Q year = (Q combustion + Q radiation) + Q distribution + Q N(useful)
Boiler losses consist of
- ...combustion loss.
It arises during about 17% of the year, i.e. about 1500 hours. The level of loss shows how good a manfacturer can extract heat from the stream of hot gas. This property is component-related and thus almost beyond modification, but can change negatively because of soot deposits on the inside of the boiler due to burners burning with a yellow flame. You can reduce combustion loss of older boilers by fitting extra flow resistance plates. The technically measured value is called burning efficiency.
Improvement options:
- Lower flame strength (which results in a relative increase in heat exchange surface)
- Blue-flame burner (less unburned gases)
- Air-Offgas system (cheap, because then you have off-gas values which are 5 points better)
- Change the heat exchangers in the boiler.
- ...loss by radiation from all hot components
Improvement options:
- Full boiler insulation
- 100% pipe insulation
A combination of these improvement options is possible.
[ Contents ]
...when the burner is off
During idling and cooling phases only Q combustion is missing in the equation shown above:
Q year = Q standby + Q distribution + Q N(useful)
or in more detail
Q year = (Q cooling + Q radiation) + Q distribution + Q N(useful)
According to the type of boiler or burner, standby losses occur:
- ...cooling down losses
by the chimney ventilation, only to be prevented by a valve in the burner or a valve in the outlet of the boiler. Extremely wasteful are athmospheric boilers.
Improvement options:
- Air-tight valve in the burner
- Off-gas valve
- Air/off-gas system (extra benefit: mandatory ventilation of the heating room can be sealed, enabling the recuperation of radiation losses for the house.)
- ...radiation losses from all hot surfaces.
These always occur if a surface is warmer than the environment (for your heating system about 8760 hours annually).
Maximum standby losses arise when generating hot water in summer when boiler and tank stay at maximum temperatures with no possibility of cooling the boiler by taking off useful heat.
Improvement options:
- Full insulation of the boiler
- 100% insulation of all pipes
- With mixers: a control to fully cool the boiler after the burner has stopped.
- Solar energy system - but operated in the right way!
In normal heating system operation, standby losses and the use of useful heat cool the system down. In a cooled system, ventilation and radiation losses tend to zero. Then the only loss is the electrical current consumption of aggregates still on.
[ Contents ]
...when the burner goes on
- Shortly after ignition, the flame becomes cooled by the material of the boiler and transfers heat (as fast as the material allows) to the cold medium on the other side of the ignition chamber. At this start-up phase, the mass of the boiler material and the boiler water take up more energy than they make available to the boiler output and consumers. This continues until a stationary condition has been reached and the energy flow to the consumer is constant. If at this moment (and this applies to all oversized and inflow-controlled systems), the differential gap of the boiler is so small that the stationary condition is not reached, or the speed of warm-up is too fast, resulting in control switch-off, a part of the output which has gone into the mass of the boiler disappears by radiation into the ventilated cellar when the burner is off. This energy is wasted, and your money too...
- In the moment when the burner starts, burner start-up losses occur in addition to the dynamic boiler losses. All car drivers will understand this: burners behave in a similar way to car engines. According to the age of the burner, start-up losses occur between 3 and 6 minutes after each start (with inferior controllers up to 40000 times a year). In this time you can only reckon with an efficiency of only ~36%. More...
The start-up phase of the part of the running time which is particularly costly.
Improvement options:
- Reduction of power output (Burner runs a longer time)
- Adjust the booiler hydraulics apropriately and add a pump controller with dT-adjustment.
- Adjust the system controller economically.
- Delay burner start-up by 15...30 minutes (cheap).
- Replace controller if older than 10 years.
- Buffer (expensive, more radiation losses and the buffer must have its own charge controller - especially complicated with solar).
You will probably recognize that the stand-by losses due to short burner running times are the most expensive: you get no useful heat and generate these stand-by losses with efficiencies of only 36%. If you manage to cut these out, you are money in.
[ Contents ]
3. Distribution and useful heat
- Distribution losses
are caused by radiation loss from pipes and pumps together with the current they consume.
Consider this: Pumps pump boiler output into the house, necessary while the burner is generating heat. But what happens when the burner is off? Almost always the pump continues to run - only benefiting energy providers such as RWE and EON...
Improvement options:
- Time-triggered pump (staircase lighting relay)
- Temperature-triggered pump (pipe-mounted sensor)
- Delta-T controlled pumpe (best option)
- 100% insulation of the pipes
- Useful heat
is what is left and actually arrives at your radiators. If you have a good, optimimized system with an annual utilisation ratio of 90%, you can thank your lucky stars because in a standard heating and a control system you will only get 60%!
Improvement options:
- New control system results in cheaper heating: a return-flow controller depending from outside temperature.
- 100% pipe insulation outside the heated rooms
Losses from the total of energy applied, which are a function of both temperature and components, occur not only in different places but also at different times. [source: IWO, system oil heating]
[ Contents ]
4. New concept for an economic controller
Is it possible to practically apply this knowledge using conventional control systems from recent centuries?
Only partially or at great expense!
Conventional controls suffer because
- ...they are forced to maintain a high outflow temperature (higher losses) since systems are not hydraulically balanced and not matched to boiler size.
- ...boilers are not run at their optimum operating point.
- ...they shut down boilers when still hot instead of running them down to room temperature.
- ...they are unable to sufficiently take acount of foreign heat sources in the rooms. Mostly they achieve this by a room sensor, which is only able to measure in one of the rooms.
- ...system parts are almost always supplied by mixers and built-in pumps, which result in high annual consumption of current.
Here is a controller which consequently avoids financial and heat losses:
- One requirement is an hydraulically correctly balanced system.
- Only a single central pump with appropriate hydraulic electricity-saving control.
- Controlled firstly via backflow temperature and then via external temperature.
- Successful avoidance of frequent starts through use of the total heat capacity of the system: max. 20 starts per day.
- Always achieves an annual utilisation ratio above 90% of the upper heating value.
Compare: in spite of advertising claims to the contrary (109% of lower heating value NUR), even state-of-the-art condensing boilers can at best achieve only 92% upper heating value (normally only 86%). This is according to a study from University of Wolfenbüttel.
The one and only product meeting these criteria is a return-flow controller depending from outside temperature.
|
[ Contents ]
5. Idea: losses make good feetwarmers
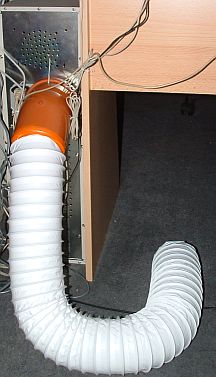
Outlet hose for re-chanelling air from your PC [Photo: L.Spangenberg]
|
Re-chanelling air from your PC:
Idea and realisation by Lutz Spangenberg. Thanks!
'The 100mm diameter fitting is simply fixed by a single wire. I drilled a small hole in the fitting, pulled through a wire with a knot at the other end, and fixed the fitting to a hole in the PC housing. The weight of the fitting and hose is sufficient to make a seal with the ventilation outlet.
This a bit make-do, but can be removed quickly in hot weather. This idea, which started as an experiment has become something I'd prefer not to do without.'
What you need:
- Wire
- 100mm diameter fitting or round pipe, 45º recommended
- 1m outlet hose 100mm diameter for dryer
- Foam for sealing
|
|